In recent years, turbine inlet air chilling (TIAC) has become a highly reliable method of enhancing power plant performance by increasing the output and efficiency of combustion turbines during periods of high ambient temperature. This is typically achieved either through mechanical or absorption chilling and involves supplying chilled water (or an alternative fluid) to the heat exchanger in the filter house of the combustion turbine, thereby cooling the inlet air which raises its density and increases mass flow rate through the compressor.
Typically, TIAC provides gross output gains of 10 – 35% for gas turbines at design conditions. However, in many instances a large portion of that gain is re-consumed by the chiller plant itself to drive additional cooling – a term commonly referred to as the auxiliary load. The net plant output (actual electricity available to deliver) is the gross plant output minus the auxiliary load.
Combining TIAC with thermal energy storage (TES) can serve as a solution to this problem by shifting some or all of the auxiliary load to off-peak times so that more power is available for the plant to sell or use when it is most valuable during the day. A Full Shift system transfers the auxiliary load almost completely to off-peak hours (except for pumps to move the water) whereas a Partial Shift system distributes the auxiliary load throughout the day. This reduces but doesn’t eliminate the on-peak auxiliary load requirement. TES provide a number of benefits that enable operators to increase net plant output, potentially increase net plant efficiency, and lower capital and operating costs.
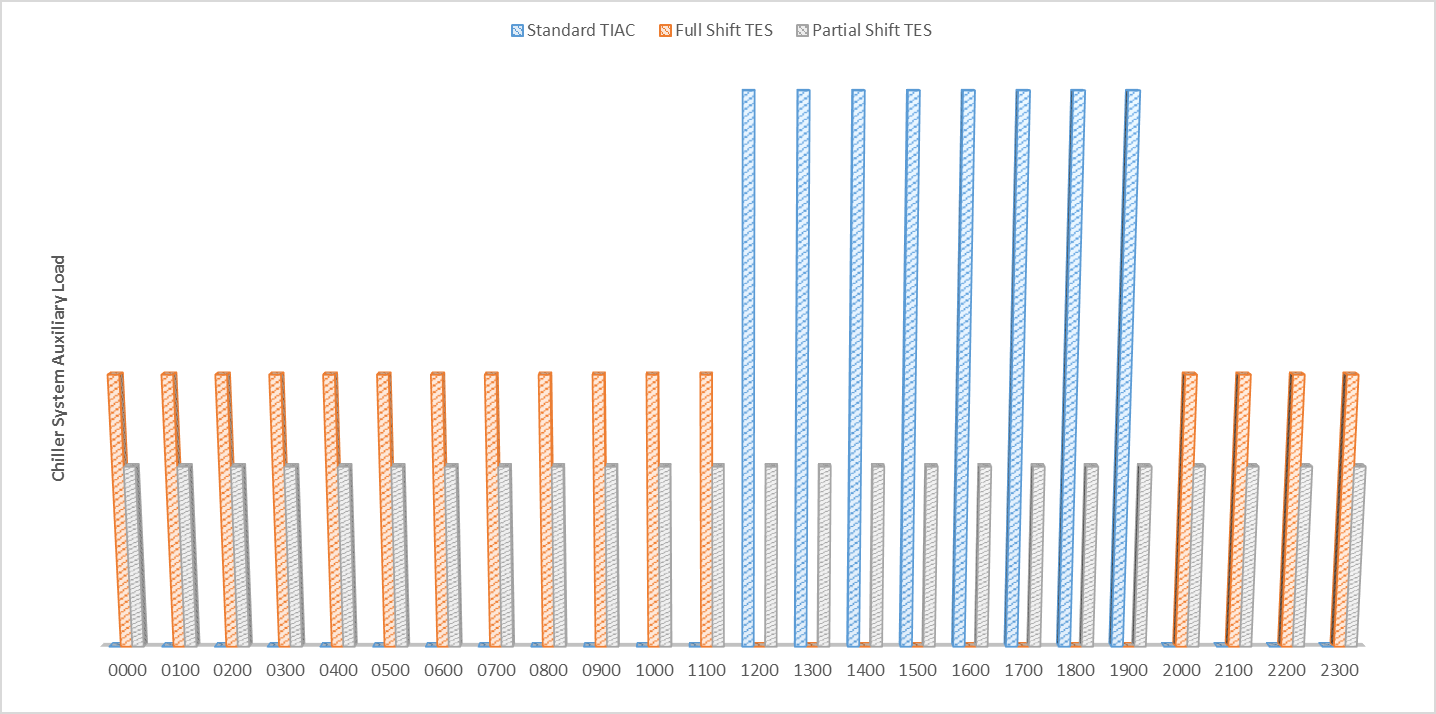
The chart demonstrates the differences in auxiliary load for three systems: Standard TIAC, Partial Shift TES, and Full Shift TES. The On-Peak duration in this example is from 12pm to 7pm.
How it Works
The term Energy Storage encompasses a wide variety of technologies, including thermal storage (ice and water), batteries, pumped hydro, flywheels, compressed air, etc. While the technologies and their components are diverse, they all rely on the same fundamental concept: Consume energy when it is abundant and/or low-cost and then use it when energy is scarce and/or higher cost. Typically, this concept translates into using energy (electricity) at night and then producing, or enabling higher production of energy (electricity) during the day.
In the case of TES systems, electricity is consumed at night (off-peak) to run vapor compression chillers and create cold water. A storage tank is “charged” with cold water by pumping it in to the bottom and pulling the warmer water off the top to be chilled, where it then returns to the bottom of the tank. When the tank is comprised of only cold water the charging cycle is complete. During the day (on-peak) all or some of the chillers are de-energized and the cold water created overnight is used to chill the inlet air. This creates a lower auxiliary load which results in a higher net plant output. Cold water is pulled out of the bottom of the tank and warm water is returned to the top. When the tank is comprised of only warm water, the discharge cycle is complete.
In addition to increasing the combined power output of the combustion turbines, TES systems can often lead to a reduction in capital costs by minimizing the size of the chiller plant – although this is a function of how many hours of chilling are required on a daily basis. Additionally, with chiller plants operating during off-peak times at night with correspondingly lower ambient temperatures, chiller plants can operate more efficiently. This benefit is magnified in the case of air-cooled systems.
Overall, TIAC by itself can cost anywhere from $150 – $700/kW – and while its effectiveness is highly dependent on specific design parameters and operating scenarios, using TES in conjunction with TIAC can potentially reduce those figures by up to 40%.
Considerations for Combining TIAC with TES
When evaluating the feasibility of combining TES with TIAC, operators should consider a number of factors. Some of these include:
Availability – TES design is based on the simple premise that there will be hours in the cycle to build up capacity for the next peak period. The shorter the peak, the less costly a TIAC-TES system will be because more hours to build capacity for the next day will be available. Ultimately, TES allows for the size of the chiller plant to be kept to an absolute minimum.
Footprint – TIAC systems require space onsite for the chiller plant and also at the filter house for a heat exchanger. TES systems require additional space for the storage tank, which may be problematic for some facilities.
Winterization – TES separates chilled water from hot water returning from the filter house via stratification. However, many TIAC systems are designed using water/glycol to prevent freezing of the liquid in the coils and bursting of the tubes in the coils. Water/glycol storage is not feasible because the same way it works to provide an anti-freeze capability reduces its ability to stratify. Therefore alternative freeze protection methods are required. A typical solution is to provide a glycol purge to the coils as part of a winterization procedure.
Optimization – TES systems have multiple variables which can be manipulated to achieve specific plant goals. Tradeoffs and compromises will result in a customized solution that meets or exceeds the desired objectives. Stellar Energy can assist in this evaluation to ensure system parameters are minimized where necessary and optimized where important.