As the true work horses of a TIAC system, chillers are very good at moving the heat from the process water system to the heat rejection system in very large quantities as long as the variables of the process water and heat rejections systems stay within the design limits of the chillers. If these variables venture outside the design limits, the chillers can experience a condition called surge which can cause damage to the chiller’s compressor.
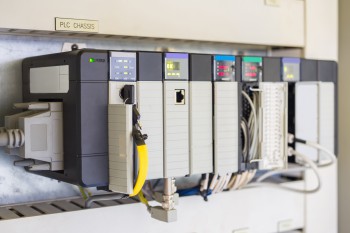
Free Risk Assessment: Is it Time to Upgrade Your Control System?
Every component of your control system – from controllers, I/O cards and network equipment to computers and software – has an expectant lifecycle. If any component of the control system is at or near its end-of-life phase, the potential risk for production shut-down is significantly increased. Therefore, it is critical to know the age of all components of your control system, whether your system hardware and software are still supported by the manufacturer and the availability of spare parts so that you can avoid costly unplanned downtime.
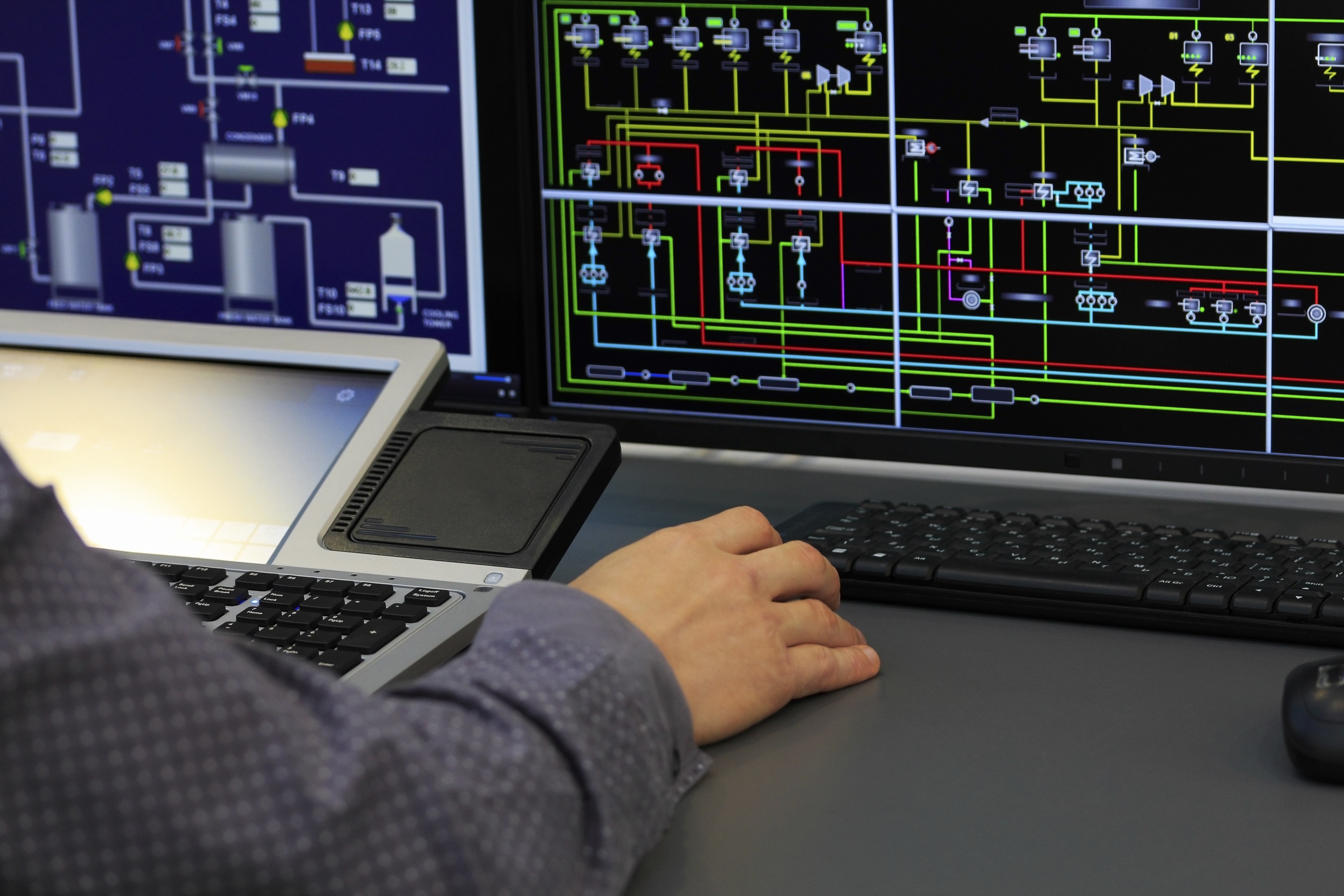
Seven Tips for Maximizing the Performance of your Chilled Water Plant
Chilled water plants are sophisticated assets comprised of mechanical and electrical systems controlled by programmable logic controllers (PLCs). They play a critical role in the operation of a wide range of facilities, including power plants, industrial facilities and data centers, and are often designed to function with minimal operator interaction. However, even the most intelligent systems degrade over time and require some amount of service and tuning to maintain optimal performance.
Here are some preventative maintenance measures you can take to ensure that your chilled water system is always operating in an efficient, safe and reliable manner while maintaining peak performance.
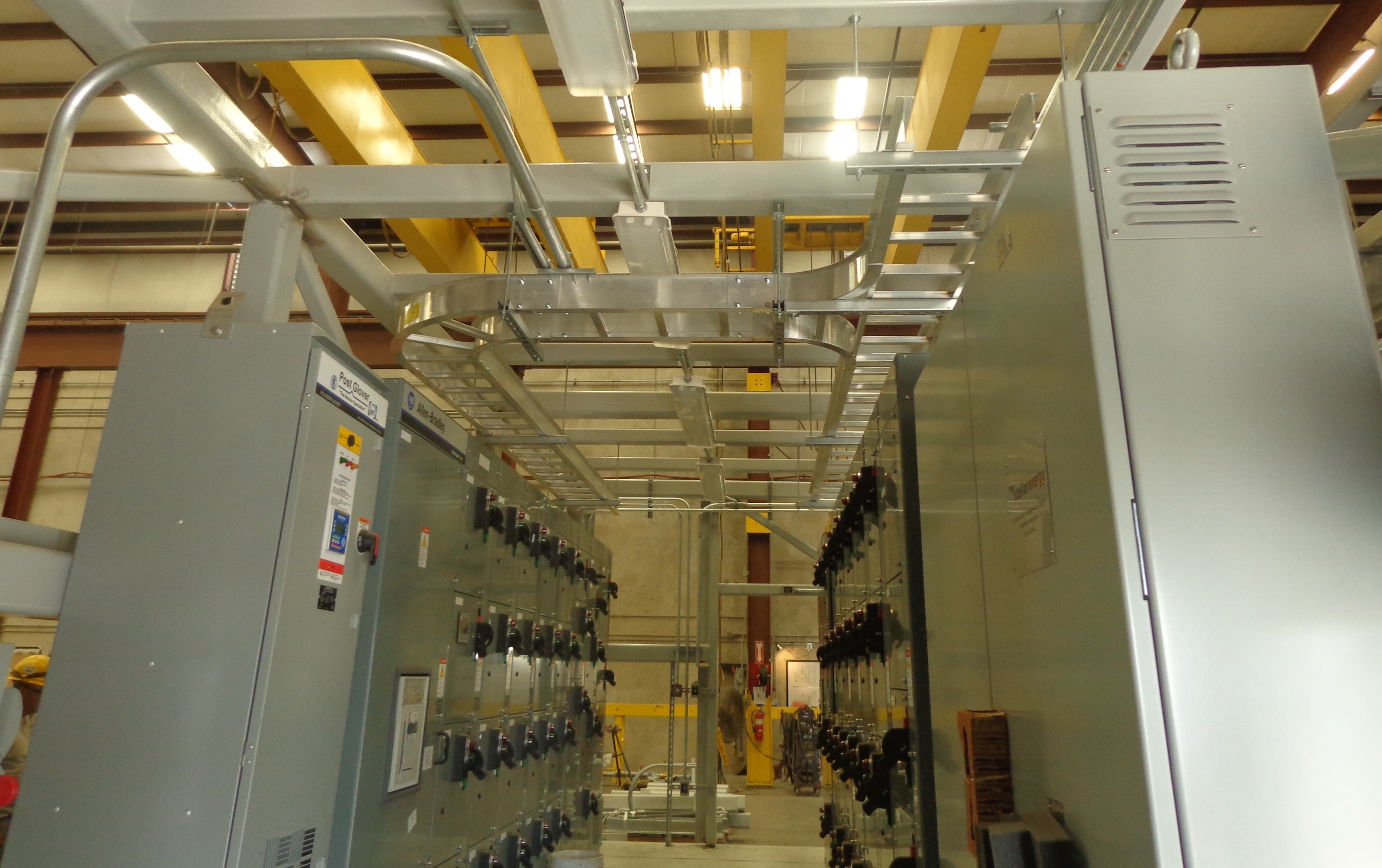
Addressing Electrical Space Requirements in Modular Energy Plant Design
“Sure, we have plenty of space….”
Often times that is the response we receive when we have to add equipment to an existing, or nearly complete design. While there may be physical space for the equipment in question, the space requirements imposed by the National Electrical Code or other regulations around electrical equipment often make a seemingly ample-sized space just too small. Some reasons for regulatory requirements for space around electrical and other equipment include: means of egress from an enclosed space in the event of a fire, door swing clearance for protection of personnel, electrical working clearances for the protection of electrical workers, fire safety equipment access (such as fire extinguishers), and equipment operational space where manual manipulation of equipment is necessary for operations personnel.
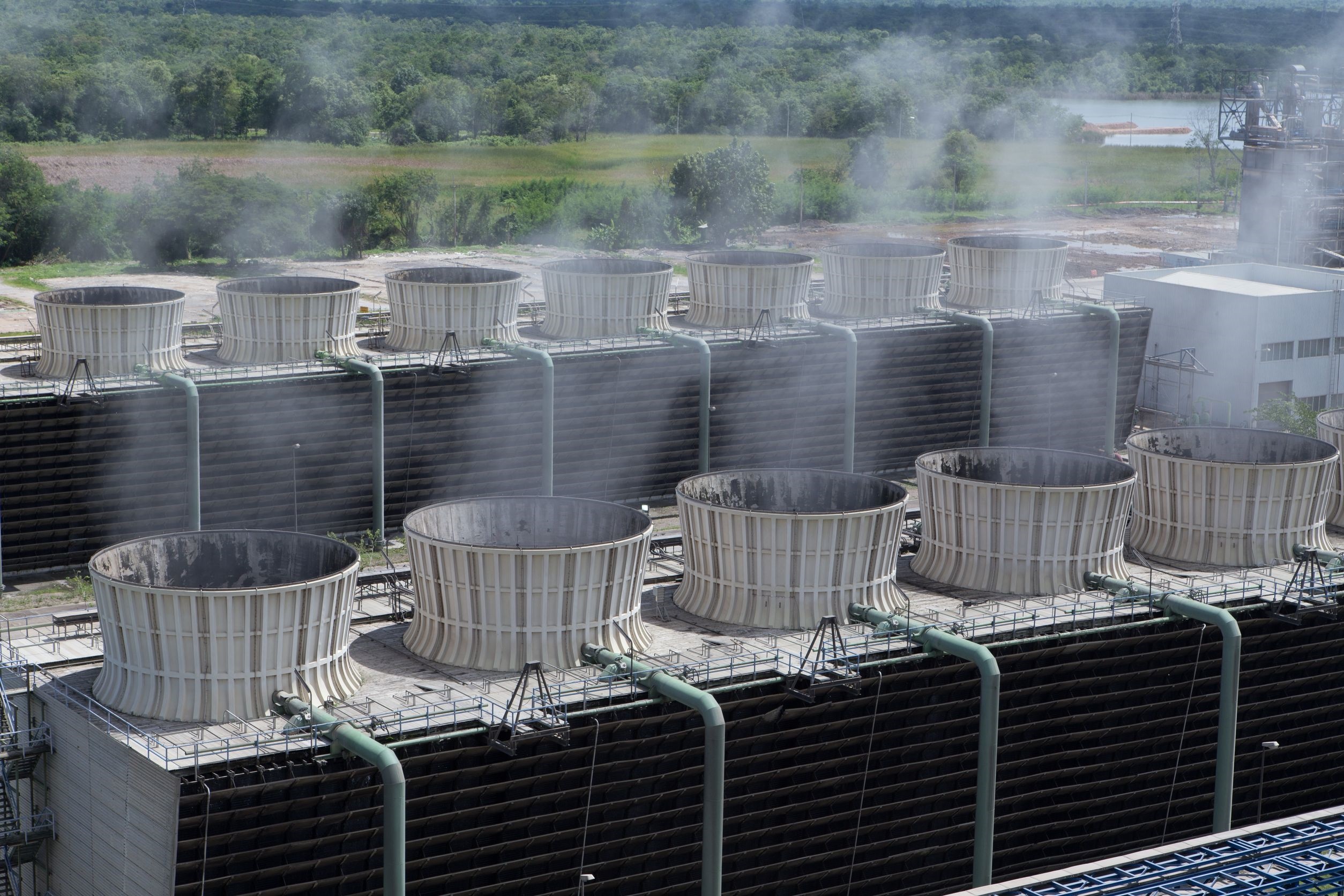
Three Key Considerations When Using Water as a Heat Transfer Medium
Water (H2O), the most abundant substance on earth, is also a universal solvent. From rivers and lakes to seas and oceans, water is the main ingredient but its composition varies because of its solvent properties. As water falls through the air, it absorbs gases and picks up particulates such as dust and pollen. Then, as it trickles down through soil and rocks, it dissolves minerals along the way. As a result, water quality varies greatly both regionally and seasonally.

Water vapor rises from cooling towers at power plants, hospitals, hotels and other large facilities.
Water is also a highly effective heat transfer medium. Heat transfer is the process whereby thermal energy or heat moves from one body or substance to another, and from hot to cold. We’ve all noticed the large plumes rising from a hospital, hotel or a power plant.
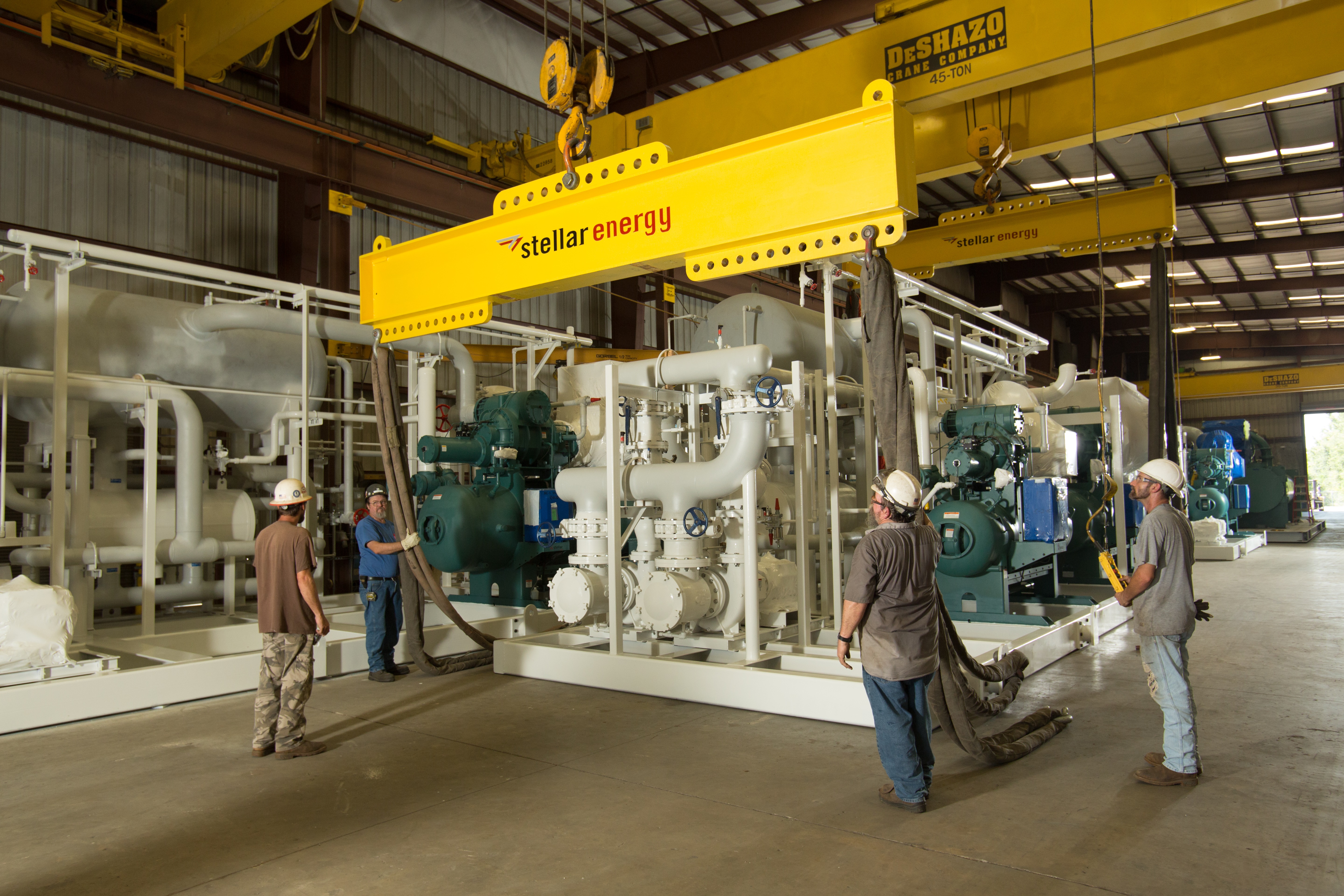
10 Benefits of Modular Fabrication
The modular chiller plant is a self-contained chilled water production system. An efficient and affordable alternative to the traditional stick-built chiller plant, the modular chiller plant works equally well in a building mechanical room without an enclosure, and in an open environment with an enclosure to protect the components from the elements.
The modular chiller plant is pre-engineered and fabricated with all system components. Packaged in a skid, the module is pre-piped, wired, tested and shipped to the job site where the water and power connections are made.
Modular does not mean one-size-fits-all. The modular chiller plant can be designed for primary secondary, variable primary or fixed primary operation, and it can be customized to special engineering requirements for component type, manufacturer and model.